
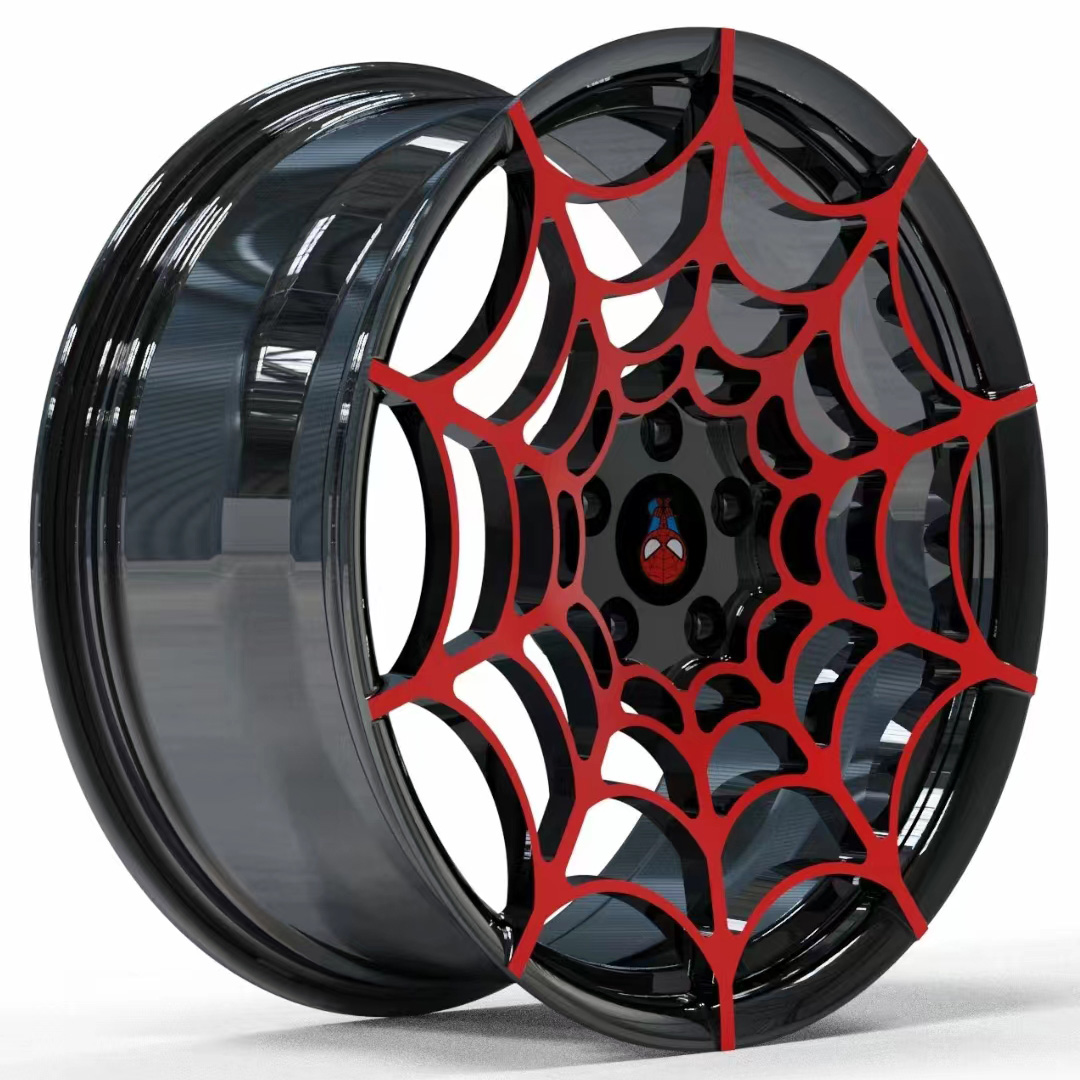
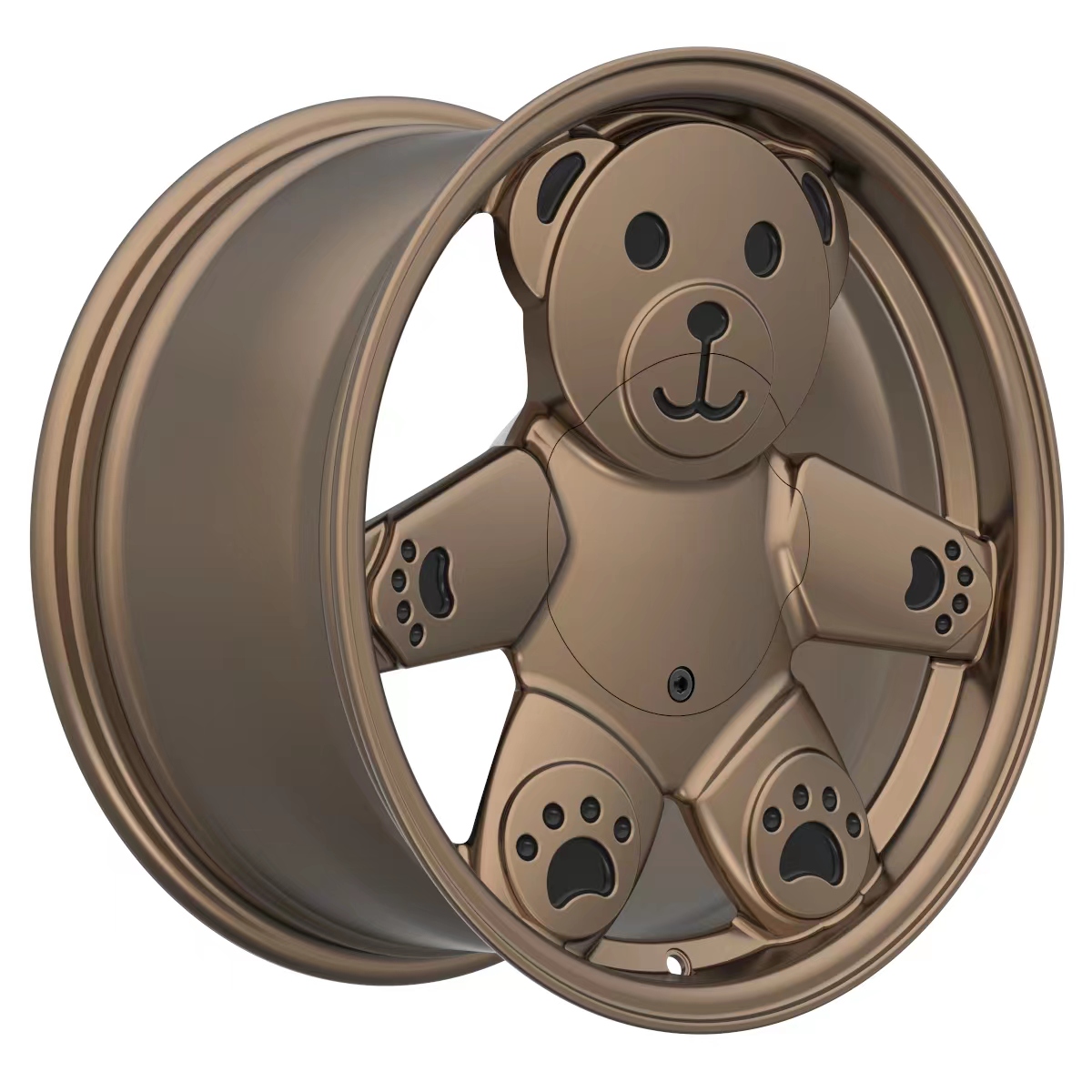
Custom forged design
SPECIFICATIONS
Custom forged wheels are high-performance, lightweight wheels created using a specific manufacturing process that involves the shaping of metal under intense heat and pressure. This process ensures the wheels are both strong and lightweight, making them ideal for high-performance vehicles, sports cars, and luxury applications. Custom forged wheels are typically made to order, allowing for personalized designs, fitments, and finishes.
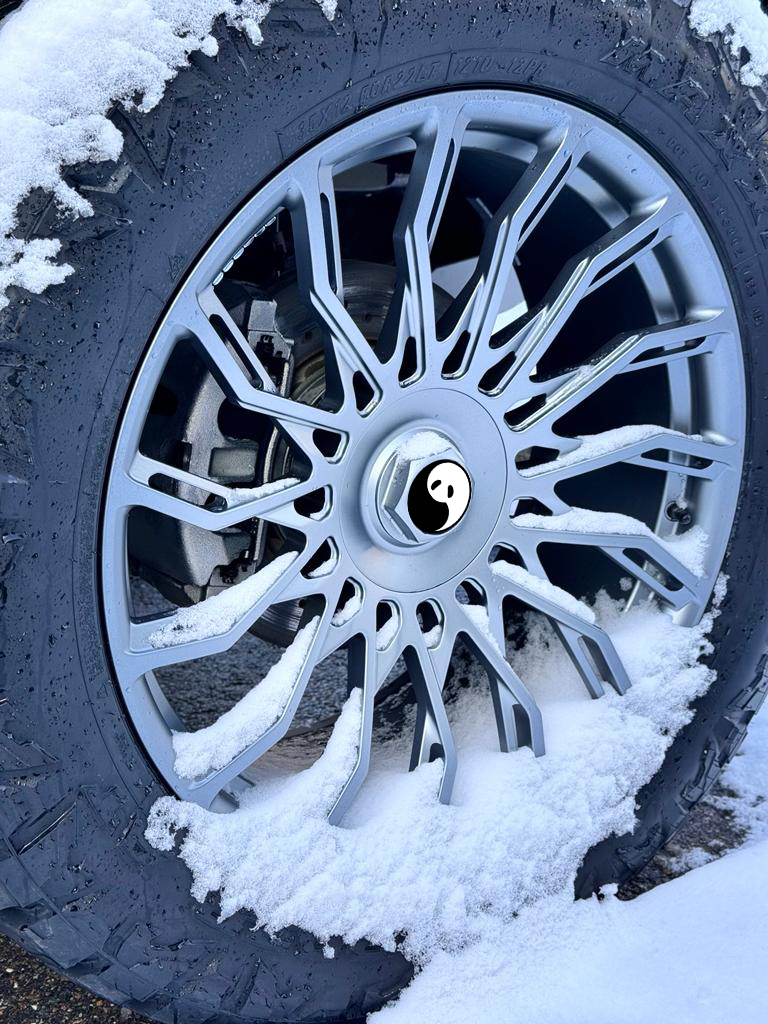
monobloMocks
SPECIFICATIONS
- Monoblock means the entire wheel is forged from a single piece of material, unlike multi-piece wheels, which are made from two or more parts (e.g., the barrel and the face of the wheel).
- This construction leads to a more uniform strength distribution, and there’s no potential for the joints to weaken over time, as is the case with multi-piece wheels.
Monoblock wheels typically feature intricate designs that save weight in non-critical areas, further improving performance by reducing rotational mass.
The forging process (using high pressure and heat) results in a denser and stronger material, making the wheel both lighter and stronger than cast wheels or multi-piece wheels.
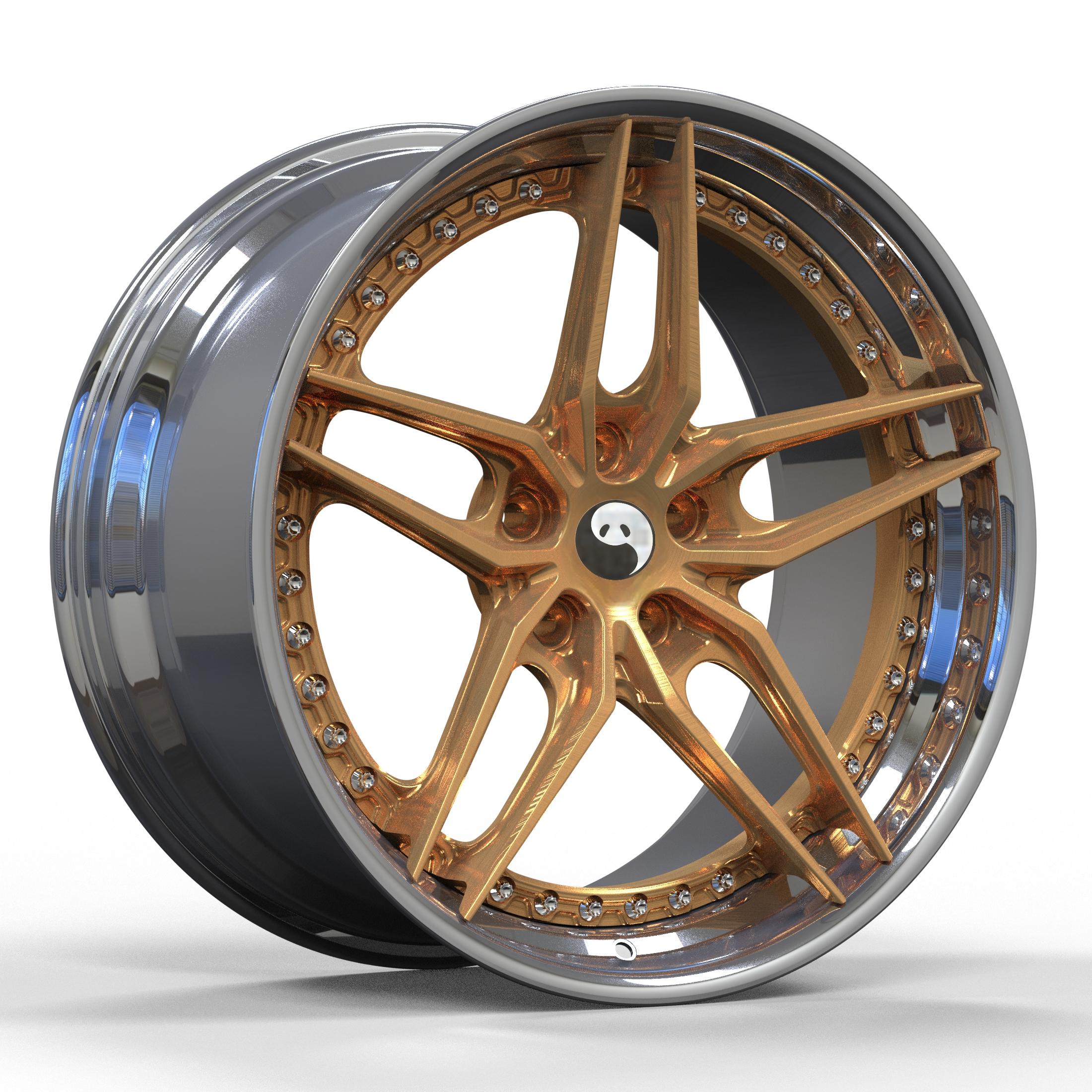
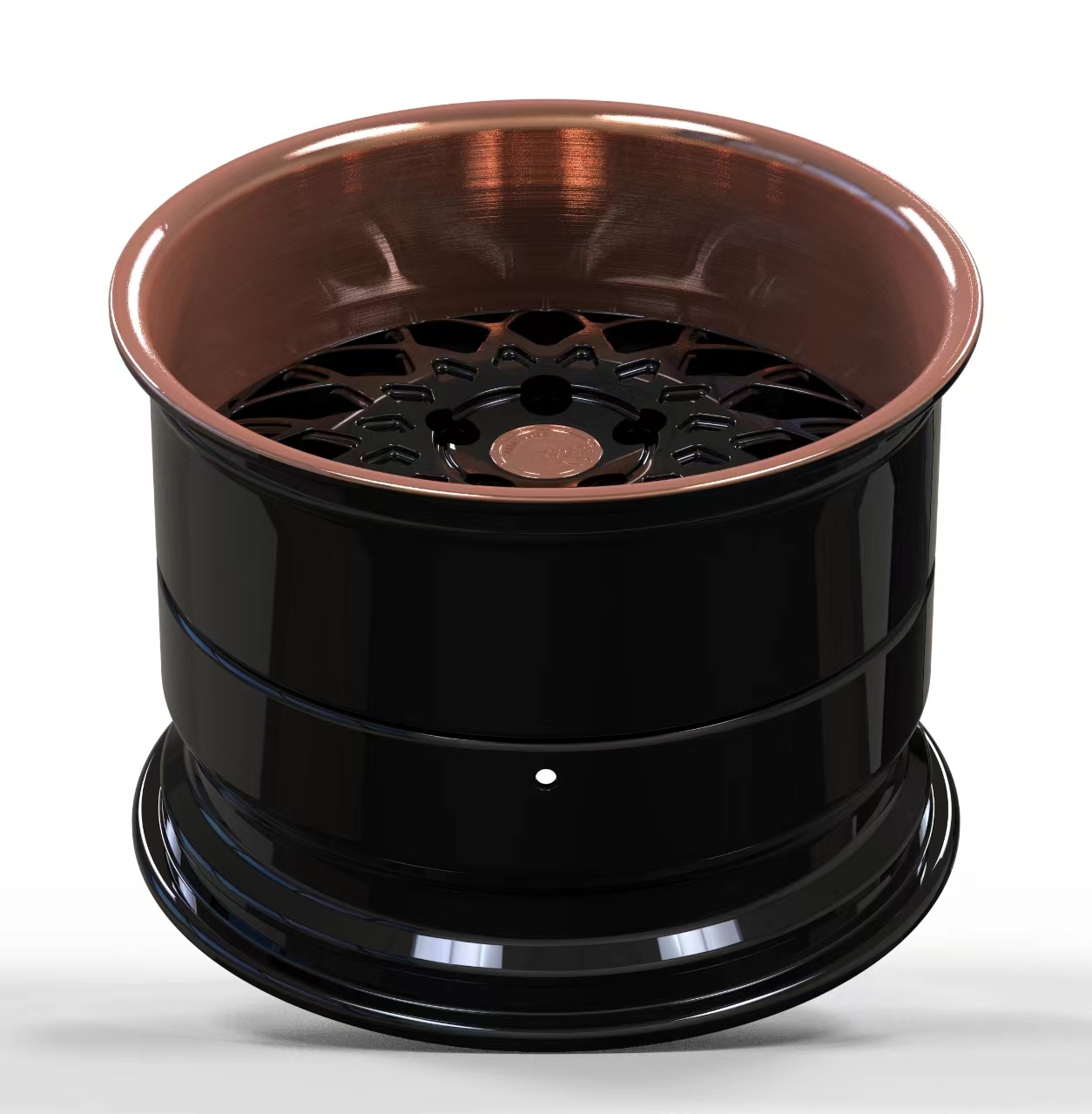
2-piece/3-piece
SPECIFICATIONS
The Center Disc: This is the face of the wheel that connects to the hub of the vehicle and provides the main design aesthetic. The Inner Barrel: This forms the inner part of the wheel and determines the backspacing and offset. The Outer Lip (or Outer Barrel): This contributes to the wheel’s appearance and width, as well as its overall stance.
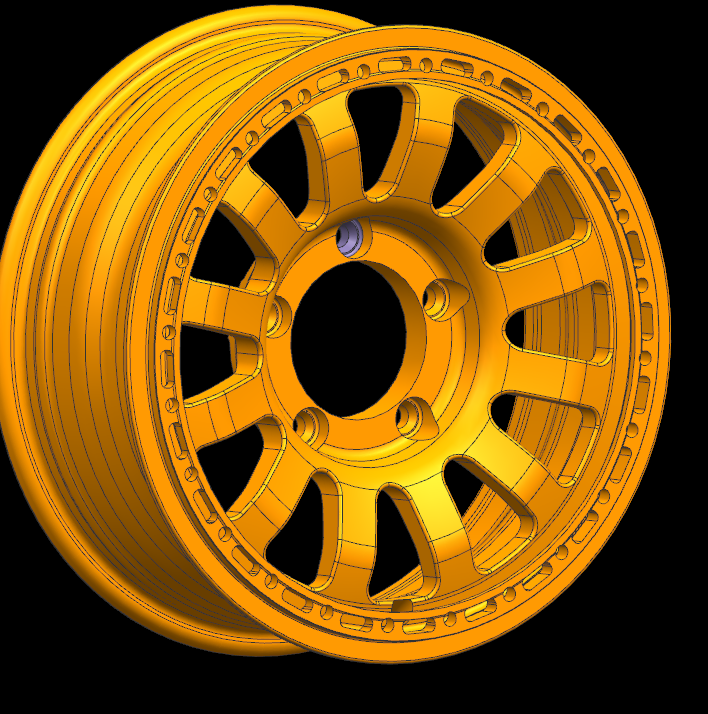
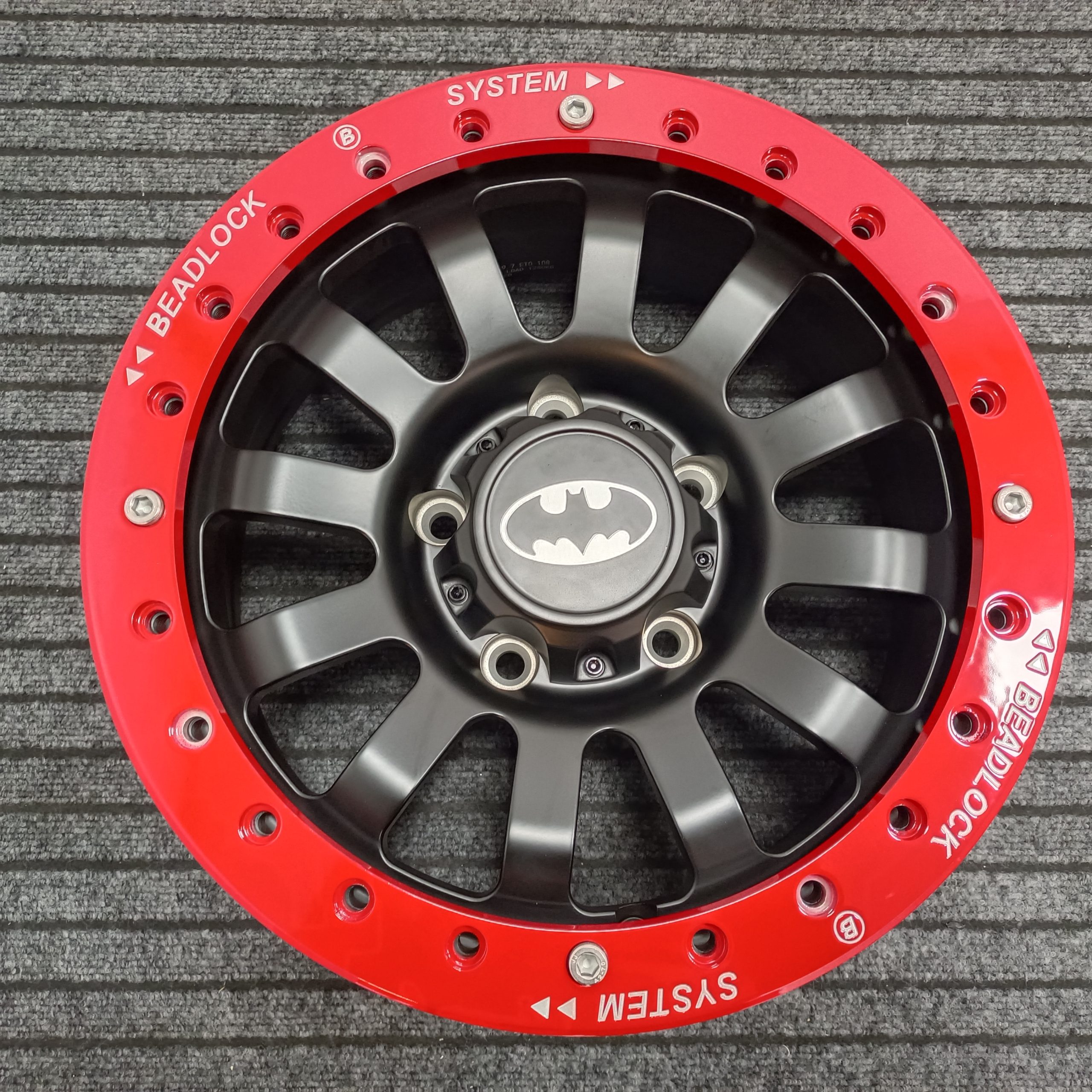